Railway sleepers made from recycled plastic installed at Richmond Train Station
The sleepers will last three times longer than traditional railway sleepers and are made from recycled plastic sourced in Australia, including vineyard covers and cotton bale wraps.
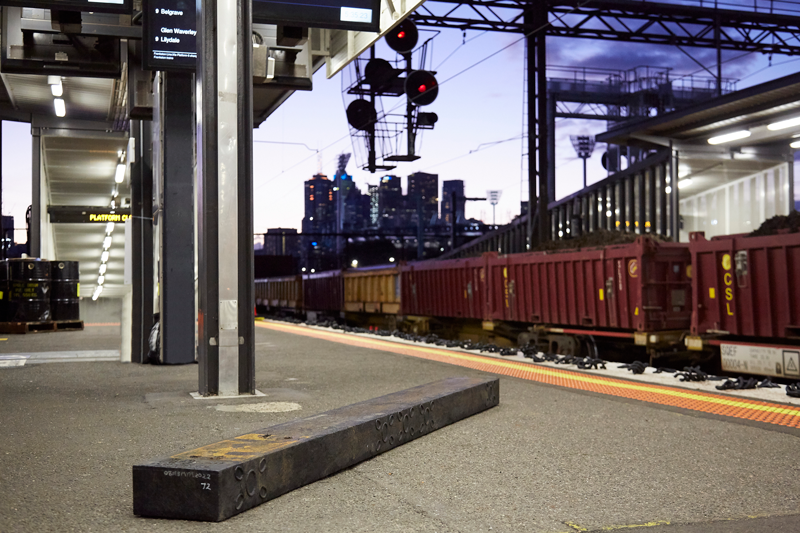
In a first for Victoria’s public transport system, trains travelling through Richmond are now running on railway sleepers made from recycled plastic.
190 of the sleepers were installed at Richmond Train Station as part of maintenance work done by Metro Trains over the weekend of 22–23 June.
It is the first time the metropolitan train network has used the innovative sleepers, which are comprised of 85% recycled plastic waste.
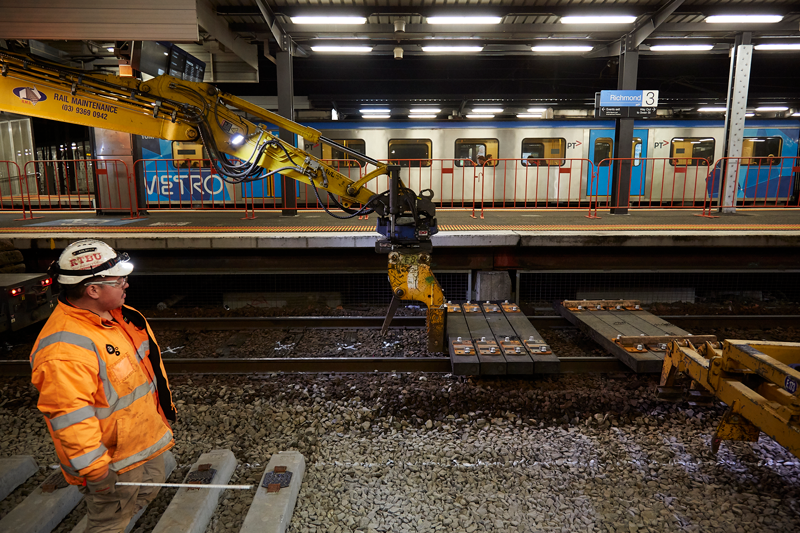
The sleepers have already been installed with great success at a handful of different tourist and heritage railways in Victoria including Puffing Billy, Walhalla and Castlemaine.
The installation at Richmond is part of a trial being conducted with Metro Trains. If the trial is successful the sleepers could potentially be rolled out across the metropolitan train network as part of future rail upgrades.
The Duratrack composite plastic sleepers are produced in Mildura by Integrated Recycling and contain a mix of polystyrene and agricultural plastic waste, including cotton bale wrap, vineyard covers and pipe from the mining industry, which was previously unable to be recycled and sent to landfill. All the recycled plastic used in the sleepers is sourced in Australia.
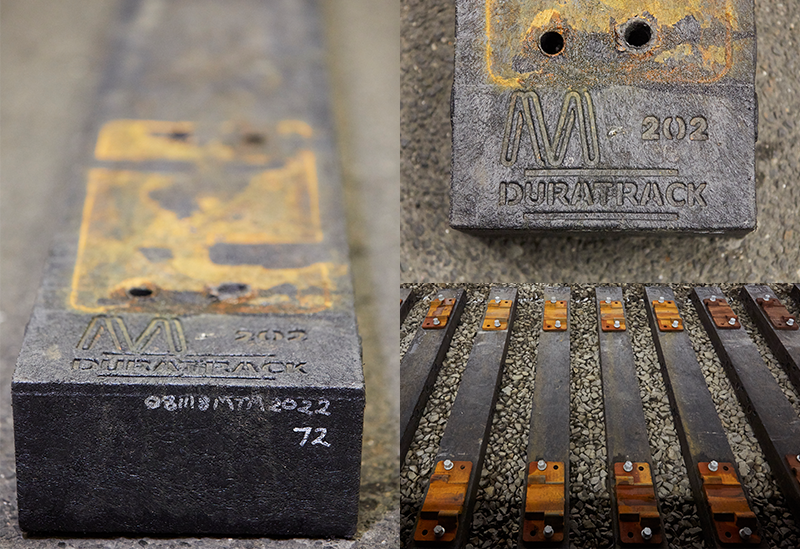
The sleepers require far less maintenance and have a lifespan of up to 50 years – three times longer than traditional timber sleepers. At the end of their lifetime the sleepers will be recycled into new sleepers, fulfilling the promise of a truly circular economy.
The environmental benefits of using the sleepers are clear as they reduce the need for timber resources, reduce concrete production (the second-largest carbon emitter in the world) and meaningfully recycle plastic waste.
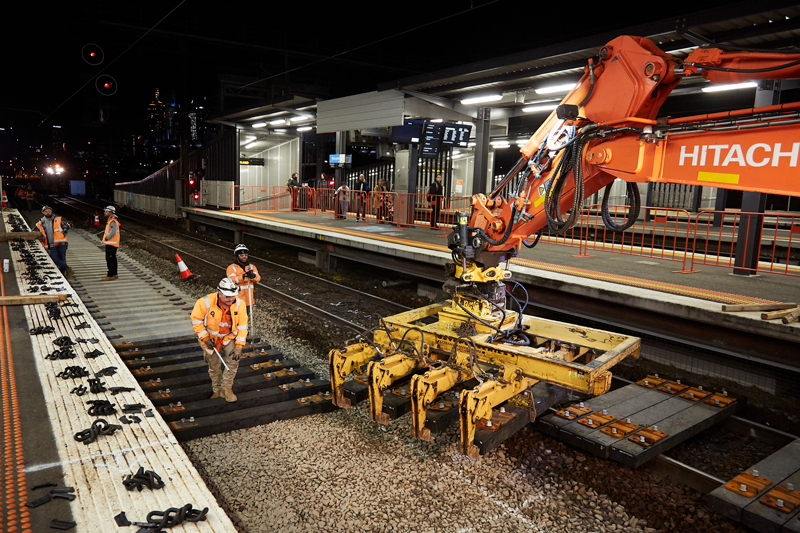
Compared to concrete, timber or steel sleepers, the sleepers also require less energy and resources to manufacture, thereby producing significantly less greenhouse gases.
For every kilometre of track installed with the sleepers, 64 tonnes of plastic waste that would have otherwise gone to landfill is recycled.
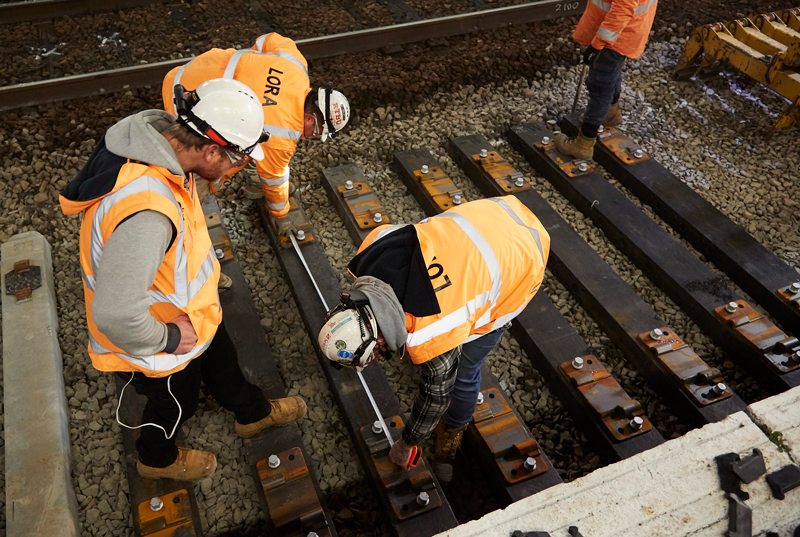
The ground-breaking railway sleepers are the result of nearly four years of research and product development led by Integrated Recycling and Monash Institute of Railway Technology – and supported by Sustainability Victoria through two Research, Development and Demonstration grants and a Resource Recovery Infrastructure Fund grant totalling $630,000.
Integrated Recycling are also trialing the sleepers with V-Line, with installation planned for July 2019.
-
[Ambient music playing]
[Images of railway sleepers being installed at Richmond Station]
Screen text: Stephen Webster, General Manager, Integrated Recycling
“The opportunity for a recycled plastic sleeper in railways is almost unheard of.”
Screen text: Graham Tew, Research Manager, Monash Institute of Railway Technology
{Images of sleepers being tested at Monash Institute of Railway Technology}
“Most people would have said recycled plastic isn't going to be strong enough to support the loads under mainline operations.”
[Images of railway sleepers being installed at Richmond Station]
Screen text: Catherine Baxter, Chief Operating Officer, Metro Trains Melbourne
[Images of Catherine Baxter at Southern Cross Station]
[Images of polystyrene and plastic waste]
“The more I dug into it, the more I realised this is a real game changer.”
“We've got a lot of plastic waste going to landfill, and here's something that's using 85% plastic.”
“And it looks like it has a longer life than wooden sleepers.”
[Music playing]
Screen text: Demonstrating Circular Design
(Aerial images of Mildura}
Screen text: Concept
Screen text: Stephen Webster, General Manager, Integrated Recycling
[Images of Stephen Webster inside the factory with plastic waste in the background]
“The Duratrack sleeper story started back in 2014, when Public Transport Victoria wanted to find a substitute for timber sleepers.”
“The issue with timber railway sleepers is their relatively short life and the dwindling supplies of quality timber.”
[Images of sleepers being made in the factory]
“Integrated Recycling lives in the circular economy.”
“And that means that we take materials that have already had a primary use, like the vine covers that are behind us.”
[Images of Stephen Webster inside the factory with plastic waste in the background]
“They've already had their life on the vines. They've enabled the growers to grow grapes. We then use it. It becomes part of the formulation for making Duratrack railway sleepers.”
“For us to be able to develop that, we needed partners in this journey. Sustainability Victoria's contribution was invaluable.”
[Images of trains going over the plastic sleepers at Richmond station]
“The research grant that it gave to Monash University, to enable that analysis of flexible plastics in a railway sleeper environment product, was critical.”
[Images of sleepers being tested at Monash Institute of Railway Technology]
Screen text: Research
Screen text: Graham Tew, Research Manager, Monash Institute of Railway Technology
“Welcome to our mechanical testing facility.”
“The purpose of this test is to assess the structural capacity of the material.”
“Most railways and quite risk-averse.”
“Fundamentally, the current mixes well and truly exceed the requirements of any of the standards worldwide.”
[Images of trains going over the plastic sleepers at Richmond station]
[Images of Catherine Baxter at Southern Cross Station]
Screen text: Catherine Baxter, Chief Operating Officer, Metro Trains Melbourne
“We change out thousands of sleepers every year.”
“So, this could be a real alternative for us, and a much more environmentally friendly one.”
Screen text: Commercialisation
[Images of trains moving at Richmond station]
[Images of Stephen Webster inside the factory with plastic waste in the background]
“We want a viable product, at the end, that is purchased in quantity by the railway companies, so that we can then continue to develop this as a new industry in Australia.”
[Images of sleepers being made in the factory]
“We believe very strongly that sustainability won't occur without innovation.”
[Images of sleepers being tested at Monash Institute of Railway Technology]
Screen text: Supporting Research, Development and Demonstration
“The work that Sustainability Victoria is doing to encourage collaboration between industry and university, I would say to anybody, is absolutely vital.”
[Aerial view of Richmond train station and trains travelling through]
Screen text: Demonstrating circular design for the state of the future
Screen text: Sustainability Victoria logo and Victorian Government logos. sustainability.vic.gov.au Authorised by Sustainability Victoria, Level 28, 50 Lonsdale Street, Melbourne
[Music playing]
The project is a great example of government, industry, universities and rail authorities working together to create a circular economy through innovation – and by rethinking the way we approach everyday products.
The recycled plastic sleepers run alongside platform two at Richmond station, for anyone curious to see them in action (from behind the yellow line, of course).

We’re on the way to a future where commuters look through a train window and see recycled plastic sleepers flashing by instead of concrete or wood.
And that's something to smile about.
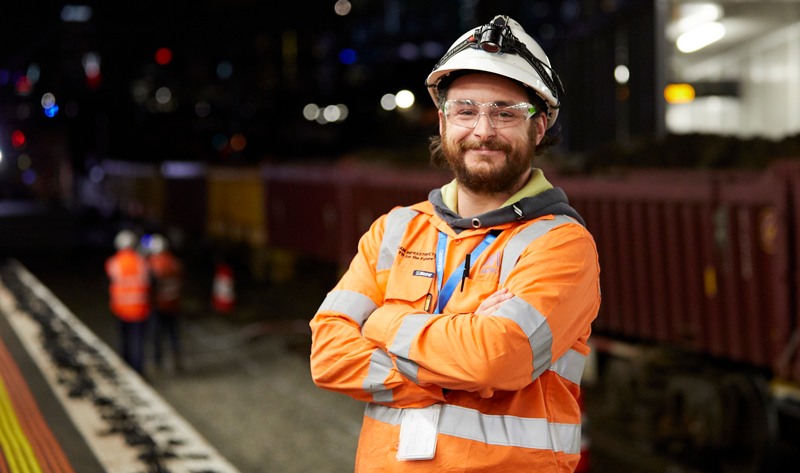