Novel ROBOVOID solution for concrete applications
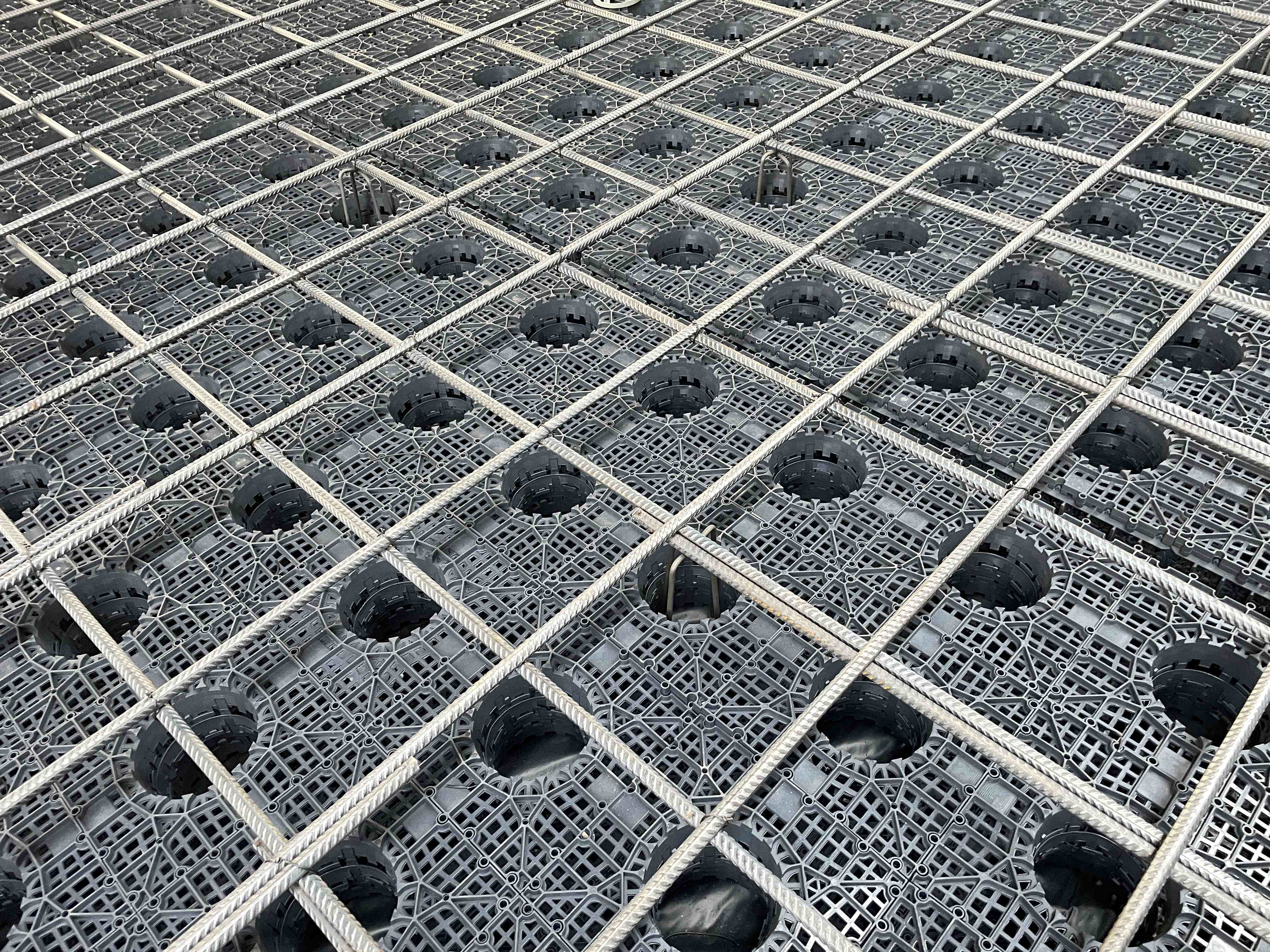
Project |
Void former for concrete structures |
Material classification |
Plastics |
Product specifications and standards |
Measured performance against relevant Australian and international standards and product specific criteria for in-situ ground slabs, precast suspended slabs, precast walls, precast facades and block walls |
Project type |
Demonstration and commercialisation |
Research result |
Previous research demonstrated the viability of using 100% recycled plastics to produce a new void former product for the construction industry in ground slabs, suspended slabs, walls and facades |
Sector |
Construction industry |
Grant recipient |
ROBOVOID Pty Ltd |
SV funding |
$175,000 R&D grant to Swinburne University of Technology $300,000 commercialisation grant to Robovoid Pty Ltd |
The product
ROBOVOID void formers are 3D geometric shapes that are placed within concrete structures. Their use reduces concrete mass and the corresponding carbon emissions. Traditional void formers are made from a range of virgin materials including polystyrene. The ROBOVOID solution uses 100% plastic waste which would otherwise end up in landfill. The void formers can be used in a broad range of construction applications.
The ROBOVOID solution can typically achieve carbon emission savings of 50%. It reduces the amount of concrete and steel needed. It creates voids that can be insulated. It is easier and quicker to install than standard concrete solutions. It can also be stacked, meaning fewer deliveries than with other void formers. It turns waste into a resource and adds to its original value.
At end of life, the void formers can be separated from the demolished concrete structure and recycled for reuse.
The product has been demonstrated in several commercial applications. This includes on Victoria’s Big Build,
The need
ROBOVOID developed its void formers in response to two fundamental societal and environmental concerns:
- carbon emissions generated through traditional concrete construction methods
- increasing amounts of plastic waste to landfill
Population growth will drive more residential and commercial construction. There is also a global push to improve energy efficiency of existing buildings. Combined, these factors will see many buildings not suitable for retrofit being demolished and rebuilt.
Concrete construction generates approximately 8 to 10% of global carbon emissions. As an industry, construction is the third largest emitter, triple that of aviation. In addition, plastic waste is a major problem globally and in Australia. Only about 13% of plastic waste is recycled in Australia.
To meet our carbon emissions targets, we must use less carbon-heavy alternatives. Not only for the construction process (embodied CO2), but for future energy efficiency (operational CO2).
'As part of GT Recycling’s expansion of its production facilities, the ROBOVOID solution was incorporated in concrete panels used for walls / retaining walls for a factory extension. A significant amount of concrete was removed from each panel, which reduced the carbon footprint for the construction.'
Developing the solution
Early research focused on using agricultural polypropylene (PP) waste (e.g. bunker tarps) that is sent to landfill at end of life.
The initial three R&D project stages included:
- Lab-based testing of the plastic material
- Analytical studies of the plastic during molding; the design of the product parts and production tooling; and how the parts functioned while in use.
- Factory-based trials of the production process and testing of the part functionality
More info on this stage can be found in this journal article.
Further research was funded through the Australian Government’s Cooperative Research Centre grants. This included:
- Structural tests to ensure reduced concrete mass did not impact the structural integrity of the concrete. The tests proved that using the ROBOVOID void former made strong connections between building elements.
- An 8m x 8m suspended slab test with the ROBOVOID system in the concrete footings, columns and the slab to test performance under load.
- Demolition and recovery of the ROBOVOID recycled plastic components from the concrete.
- Fire tests for floor and façade applications. The tests achieved a 4-hour fire rating for floor applications and certification for multi-story façades.
- Investigation into other potential plastic waste streams and mixes of plastics. Suitable alternatives include PP from Bulka Bags and Bale Twine, and mixes with PP and HDPE.
- ROBOVOID developed a semi-automated, mobile production unit to improve production capacity.
- Development of a detailed design guide for the product. This will inform designers, specifiers and users how to use the product.
The ROBOVOID team has demonstrated a commendable level of collaboration, offering a range of innovative solutions tailored to our project requirements, which help us create a fundamental shift in how infrastructure projects are delivered.
Pathway to commercialisation
In January 2023, ROBOVOID’s first demonstration project was in precast flooring at the 15-storey Satguru Residences in Mumbai, India.
ROBOVOID then installed precast panels for a factory extension at GT Recycling in Geelong, Victoria. The project used plastic recycled by GT itself. Using the ROBOVOID system reduced deliveries to site by 50%, enabling further carbon emission and logistics savings.
In June 2024, ROBOVOID was installed in a section of the ground slab at the new Keon Park Railway Station in Melbourne. There was a 38% reduction in concrete compared with a traditional concrete slab of the same thickness, when ROBOVOID was used. Carbon emissions were significantly lowered for this build.
Having completed design, development and testing phases, ROBOVOID is now offering its product more widely. Target markets include Victoria’s level crossing removal and other Big Build projects.