From trial to reality: recycled glass and plastic in asphalt roads
Downer Group partnered with Hume City Council, Close the Loop and REDcycle in 2018 to develop the first Australian road using a newly developed soft plastic and glass asphalt.
The asphalt road mix uses reclaimed asphalt, toner from printer cartridges, glass fines and soft plastics.
This project is the first to be funded under the Research, Development and Demonstration Program.
We provided over $100,000 to develop the road, including:
- $40,000 to Close the Loop to purchase infrastructure to increase production of their newly developed soft plastic asphalt additive
- $67,000 to Downer to construct the road field trial.
Diverting waste from landfill
This asphalt mix uses more than 25% recycled plastic and glass that would otherwise end up in landfill, or as a pollutant in our natural environment.
On average, every 1 km of this 2-lane road has used:
- 200,000 recycled plastic bags
- 63,000 recycled glass bottles
- toner from 4500 used printer cartridges
- 250 tonnes of reclaimed asphalt road, with 20% Reclaimed Asphalt Pavement (RAP).
We estimate that 170,000 tonnes of soft plastic waste is created in Victoria each year, with only 17,000 tonnes or 10% recovered. The Victorian Market Development Strategy for Recovered Resources identifies soft plastics as a priority material because of its increasing use and low recovery rate.
Downer won the Premier’s Sustainability Award in 2019 for the development of the asphalt mix.
Close the Loop received $500,000 from our Resource Recovery Infrastructure Fund to expand operations to increase the soft plastics additive. They are investing in infrastructure that recovers 5,000 tonnes of soft plastics annually, as well as waste toner powder and engine oil, all of which can be used in asphalt road base.
Proven to perform
Downer commissioned an internal research and development program to assess the performance, occupational health and safety risks, and scalability of the plastic and glass modified asphalt.
Compared to standard VicRoads asphalt, plastic and glass modified asphalt has:
- 60% improvement in fatigue for longer life pavements
- superior deformation resistance for withstanding heavy vehicular traffic.
The successful research led Downer to construct this soft-plastic asphalt road in Craigieburn, which supported the commercialisation of the product. It’s now available across Australia, and is currently being used by seven local governments in Victoria and councils in New South Wales and South Australia.
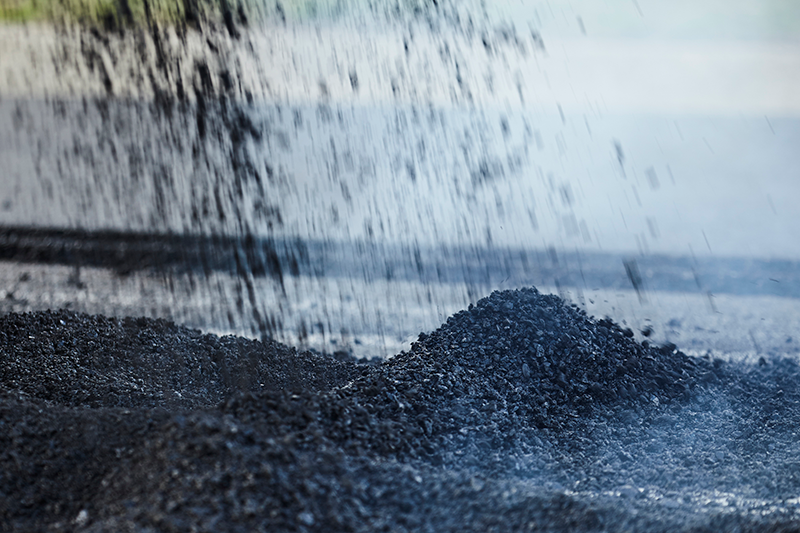
No chance of leeching microplastics
The asphalt is made up of 95% aggregate and 5% bituminous binder. The bituminous binder is the ‘glue’ that bonds and waterproofs the aggregate. The soft plastics additive melts and becomes part of the bituminous binder. Because of this process, it is not possible for the additive to separate out, creating microplastics.
This method involves returning plastic waste to its original polymer state. From there, the polymer is used as a substitute for virgin petrochemical products which are normally mined for use in road construction.
The roads industry has used virgin polymers since the 1990s. This soft plastics initiative follows a similar vein, where asphalt manufacturers modify a road construction material to improve long term performance.
Transitioning Victoria towards a circular economy
This project demonstrates circular economy at work: with plastics and glass diverted from landfill and improving road longevity and performance. The aim is to minimise waste and make the most of the resources we have.
The Victorian Government has recently launched Recycling Victoria, a 10-year plan that will invest more than $300 million to continue to transform our recycling sector.
Learn more about Recycling Victoria